Roll Selection Key Points for Tube Rolling Mills vs. Wire Rod Rolling Mills
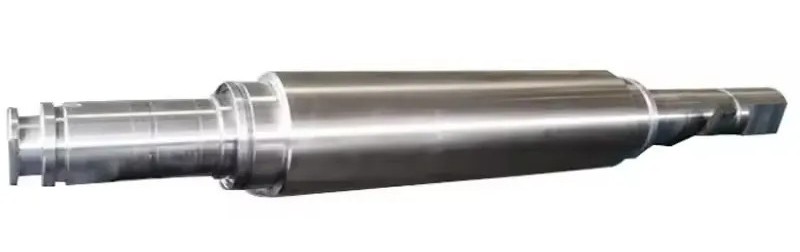
Moving on from the comparison between sheet/strip and section rolling mills, let's shift our focus to tube rolling mills and wire rod rolling mills. Each of these mill types faces its own set of unique challenges during the rolling process, which in turn leads to distinct performance requirements for their rolls.
Tube rolling mills can be categorized into hot-rolling and cold-rolling types, each with its own operational characteristics and roll material needs. In hot-rolling tube mills, work rolls utilize alloy forged steels like 42CrMo and 35CrMoV. The high strength and heat resistance of these steels enable them to adapt seamlessly to high-temperature loads. Piercing rolls, in particular, adopt tungsten-molybdenum heat-resistant steels to enhance high-temperature wear resistance, and the roll shapes are designed to conform precisely to piercing and tube-rolling processes. When it comes to cold-rolling (drawing) tube mills, hard alloys or high-speed steels are the preferred materials. Their extreme hardness and wear resistance make them perfectly suited for the production of high-precision, small-diameter tubes, and the implementation of multi-roll configurations further ensures the quality of the final product.
Similarly, wire rod rolling mills have their own distinctive features. Characterized by high-speed operation, these mills result in severe roll wear, thereby demanding strict requirements for wear resistance and thermal stability. For the roughing stands in wire rod mills, ductile iron or high-chromium cast iron rolls strike a good balance between cost and wear resistance. In contrast, the middle and finishing stands rely on hard alloys or ceramic materials to handle the rigors of high-speed operation. The use of small-diameter rolls in these mills is a strategic choice to increase speed, and the cantilever structures in finishing stands are ingeniously designed to facilitate easy replacement. Moreover, surface treatments such as carburizing, nitriding, or coating are applied, which effectively reduce friction and wear, thus extending the life of the rolls.
Post time: Jul-11-2025