Roll Selection Guidelines for Cold Rolling Mills vs. Hot Rolling Mills
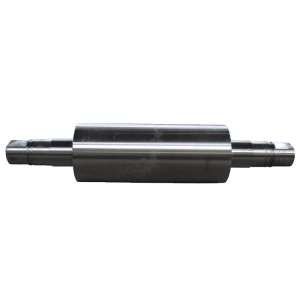
Now that we've explored the roll selection aspects of several mill types, it's time to turn our attention to the significant differences between cold rolling mills and hot rolling mills. Due to their different rolling temperatures, these two types of mills exhibit stark contrasts in roll materials, structures, and performance requirements.
Cold rolling mills operate at room temperature, a condition that brings about high rolling forces and extremely stringent demands for surface quality, dimensional accuracy, and shape. In these mills, work rolls commonly use high-carbon chromium bearing steels or alloy tool steels, with a hardness of up to HRC 60 - 65. This high hardness ensures the smoothness of cold-rolled sheets, and when it comes to producing ultra-thin strips, tungsten carbide rolls truly excel. Backup rolls, on the other hand, are made of forged steel and undergo quenching and tempering processes to enhance strength and rigidity. The implementation of multi-roll configurations is a key strategy to boost mill rigidity, which is essential for quality control. It cannot be overstated that both work and backup rolls require meticulous surface processing to ensure optimal contact and rolling performance, as even the slightest imperfection can affect the final product quality.
In contrast, hot rolling mills function in high-temperature environments, where rolls endure high temperatures, pressures, and intense wear. Under such harsh conditions, thermal stability and thermal fatigue resistance become crucial factors in roll selection. For roughing stand rolls in hot mills, cast steel or ductile iron is often used to strike a balance between strength and thermal fatigue resistance. Finishing stand rolls, however, adopt high-chromium cast iron or alloy forged steel to ensure dimensional accuracy and surface quality of the rolled products. The use of large-diameter rolls in hot mills is not arbitrary; it serves to enhance stability and load-bearing capacity. Additionally, surface cooling grooves are incorporated to strengthen cooling, which in turn reduces thermal deformation and fatigue. Through quenching and tempering treatments, rolls are given a "hard outer layer and tough core" structure, enabling them to adapt effectively to the complex working conditions in hot rolling mills.
The above content comprehensively introduces the roll selection key points for three pairs of rolling mills. If you have further questions about specific mill types or roll materials, or if you'd like to explore any aspect in more depth, feel free to let me know, and I'd be happy to provide a more in - depth analysis.
Post time: Jul-18-2025