Roll Selection Strategies for Sheet and Strip Rolling Mills vs. Section Rolling Mills
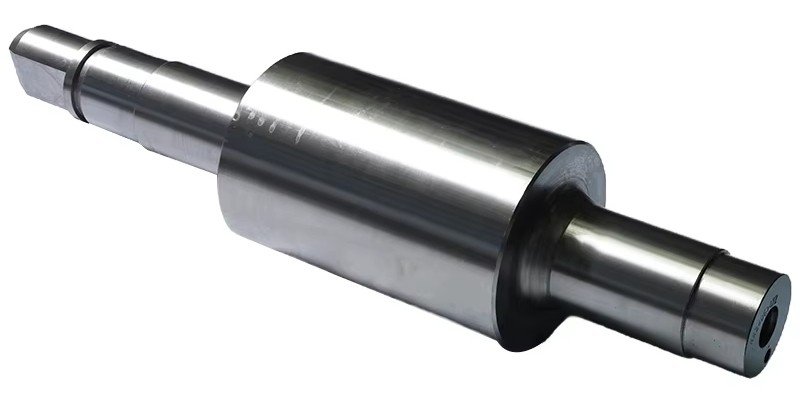
When it comes to metal rolling, the differences between sheet and strip rolling mills and section rolling mills in terms of rolling objects and processes are profound. These disparities directly translate into the need for customized roll selection approaches, which we will explore in detail.
Sheet and strip rolling mills focus on producing steel sheets and strips, where maintaining strict thickness accuracy and shape precision is of utmost importance. To meet these exacting standards, work rolls typically employ high-hardness alloy forged steels such as 9Cr2Mo and 9CrV. The excellent wear resistance and fatigue resistance of these materials act as the cornerstone for ensuring the surface quality and dimensional accuracy of the products. For applications demanding high-precision cold rolling, tungsten carbide rolls prove to be highly effective, significantly extending the service life of the rolls. On the other hand, backup rolls are usually made of forged or cast steels like 70Cr3Mo and 55Cr3. These materials provide the necessary strength and rigidity to withstand substantial rolling forces, thereby preventing work roll deformation. Structurally, the design of small-diameter work rolls serves to reduce rolling forces and optimize shape, while large-diameter backup rolls play a crucial role in enhancing rigidity. Additionally, cambered or concave rolls are employed as essential tools to assist in controlling thickness and shape, and meticulous surface finishing is indispensable throughout the process.
Section rolling mills, these mills are tasked with manufacturing complex cross-section profiles such as angle steel and channel steel. The rolling process in section mills is far from simple; during this operation, metal deformation is intricate, subjecting the rolls to strong impact forces and friction. In response to these challenging conditions, common materials for rolls in section mills include high-chromium cast iron, ductile iron, or alloy forged steel. High-chromium cast iron stands out for its superior wear resistance, making it an ideal choice for heavy-duty applications, while ductile iron offers a balanced solution between cost and performance. Roll pass designs are carefully customized according to profile cross-sections, as this is essential to ensure proper metal flow and precise forming. Roll diameters are determined by profile specifications and processes, and it's worth noting that larger diameters contribute significantly to enhancing stability. Additionally, to resist wear and maintain pass shapes over time, roll surface hardness should reach HRC 55 - 65.
Post time: Jul-04-2025