Advantages of TC Roll Rings (I)
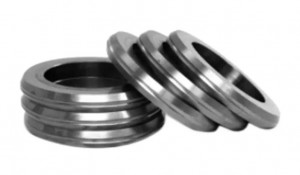
Choosing the right rolls for metal rolling operations directly affects production efficiency, product quality, and long-term costs. In the first part of this two-part series, we’ll compare tungsten carbide roll rings and ordinary rolls, focusing on the materials they process and the precision they offer.
Applicable Rolled Materials
A roll’s ability to handle metals depends largely on its properties, and here the two types differ significantly.
- Tungsten Carbide Roll Rings: Their high hardness, strong wear resistance, and good chemical stability make them ideal for tough materials. They excel at rolling high-strength metals like alloy steel, stainless steel, and bearing steel. They also meet the precision needs of non-ferrous metals such as copper and aluminum, where quality standards are strict.
- Ordinary Rolls: Made from cast iron or cast steel, these are better for less demanding tasks. They work well with low-strength metals, where surface quality isn’t a top priority. A typical use is the blooming of plain carbon structural steel, where the aim is to break down large ingots into smaller forms, not to achieve a polished finish or tight accuracy.
Rolling Precision Requirements
Precision is crucial in metal rolling, and the two rolls handle this differently.
- Tungsten Carbide Roll Rings: Their high hardness and excellent wear resistance let them stay dimensionally stable even after hours of rolling. This makes them essential in precision-critical settings, like the pre-finishing and finishing stands of high-speed wire rod mills. They produce wire rods and similar products with minimal dimensional deviation and smooth surfaces, meeting tight industry tolerances.
- Ordinary Rolls: Their lower wear resistance limits precision. Over time, rolling causes wear and deformation, making consistent dimensions hard to maintain. So they’re used in stages like rough rolling, where basic shaping prepares the material for later precise steps, rather than meeting strict tolerances.
Understanding these differences in material handling and precision helps in choosing the right roll. In part two, we’ll explore their performance under speed and load, plus long-term costs and maintenance. Stay tuned!
Post time: Jul-11-2025